Getting to Grips With Robot End-effectors – A Beginner’s Guide
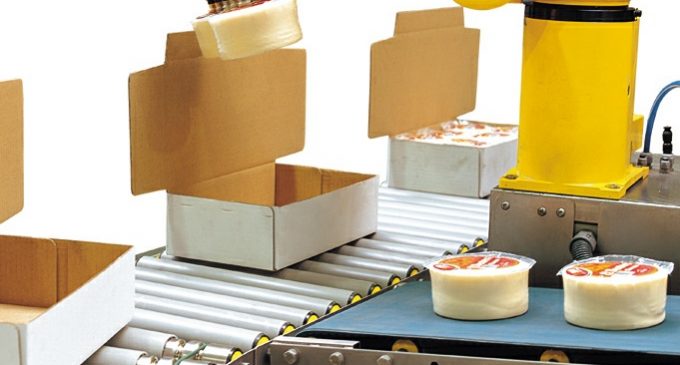
For perfectly understandable reasons, when it comes to pick and place installations for consumer goods, the robotic arm tends to attract the most attention. Although there is less of a focus on the end tooling at the tip of the arm, it is these end effectors that, when working in unison with a robotic arm, determine the precise operation that the unit performs. Pacepacker Services, an automation integrator who can provide a robotic solution to handle any food assembly or packing scenario, explores the different types of end effectors available.
“In the strict definition the end-effector means the ‘last link’, or end, of a robot arm and is the part of a robot which interacts with the work environment”. Explains Paul Wilkinson, Pacepacker’s Business Development Manager. “In a wider sense, the robotic arm resembles that of a human’s, which controls hand movements as its job is to move an end-effector from place to place.”
The selection of a specific robot model, which there are many to choose from including articulated arm, delta style or Cartesian robots, is of critical importance from both a cost and performance perspective. However, the quality of that performance will stand or fall on the choice of end effector. As Mike Wilson, Chairman of the British Automation and Robot Association (BARA) explains: “Most problems which occur in production are caused by badly-designed tooling, and not by faults in the robots.”
To put this more positively: get the design and specification of end effector right first time, and you are avoiding the majority of production problems before they materialise.
What are the Options?
Most of the end tooling for pick and place falls into one of four categories: vacuum systems, magnets, grippers and clamshell style. Each variety has particular benefits and target applications.
Vacuum gripping is the most popular form of pick and place solution. Within this range of options, compressed air is typically the most common way of generating vacuum, given that the amount of suction and configuration of valves can be tailored to the product being picked. Where more vacuum is required, a pump or even a high air-flow pump can be specified. The latter is likely to be required where, for instance, a good seal between valve and product cannot be guaranteed. [*]
When it comes to picking and placing tinplate products (including board-multipacked cans), designers can choose from electro-magnets or earth magnets.
‘Gripper’ systems probably sound more aggressive than they really are. The effect is typically one of cradling product rather than gripping it. As ever with end-effectors, the key is to strike the right balance between secure and gentle handling. If product is dented, bruised or scuffed, consumers will reject it. [**]
Clamshell-type picking tends to be used for more easily-damaged and irregularly-shaped product. A compressed air system controls the opening and closing, with bodies often tailored to the shape of the item and lined with a cushioning material such as foam. Pacepacker has designed and installed clamshell systems for small flexible packs of produce, such as peppers and onions.
The technical capabilities available for end effectors are evolving all the time. Pacepacker is an integrator of Festo Mechatronics who recently introduced a system of ‘adaptive fingers’, with ‘prehensile’ abilities not unlike an elephant’s trunk. This exciting development makes it possible to pick up delicate but irregular-shaped objects such as eggs or avocados.
Finding the Right Robot Hand For the Job
“Experience tells us that there is no substitute for trialling the specific pack and product with different robot and end effector options,” explains Paul “At Pacepacker, we have formalised this philosophy in our ‘Try Before You Buy’ commitment. Such an approach is an essential step in de-risking innovation, not only when designing customised clamshell tooling, for instance, but also when specifying the most appropriate vacuum system. Even where an apparently similar item has been matched with a particular solution in the past, those apparent similarities may prove to be deceptive in practice.”
In terms of how the specific design of an end effector is integrated into robotic pick and place, the key priority for most packers will be speed. In addition, the amount of product that can be picked in a single operation will determine cycle times. Once these are established, the payload can be determined, and the robot requirements deduced.
Pacepacker has worked as a strategic partner of FANUC for 15 years, an international supplier of a wide range of articulated-arm robots. Since June 2013, Pacepacker has also been working closely with Festo on twin-axis Cartesian-style pick and place. Both these partners offer options in the third category of robot – ‘delta’-style picking systems – where Pacepacker, too, has a proprietary system.
If more businesses are recognising the return on investment offered by robotic pick and place, this is in part because the installation cost of the robots themselves has reduced over the years. But it is also thanks to improved processes of design and specification: ensuring you have the right tooling for the product, and the right robot for the output and payload you require.
On the other hand, it can be easy to get carried away by the ‘newest’ technical developments and over specify either the robot itself or other elements in the system. “Take vision systems.” Paul explains. “There is a place in today’s market for them particularly where there is a growing number of products’ being presented to robots in erratic formats or variable positions. However where products are all in a uniform line often a simple sensor is all that’s required. By paying special attention to how the product is presented to the pick and place devise an experienced integrator will often avoid any need for over complicated vision systems.”
On many pick & place lines, tooling change will not be a major requirement. But where it is, this has to be factored in. In fact, compressed air vacuum systems can often be designed with a single coupling, and substitution times of less than a minute are likely to be dwarfed by upstream changeover requirements. “As specialists in the design of end effectors we can eliminate the need for change overs by making the end effectors multifunctional. Where interchangeability is required compressed air vacuum electronics can be quickly disconnected and re-attached using quick release couplings. These changeover times are likely to be quicker than upstream or downstream equipment.” Paul explains.
Further considerations when designing a bespoke system include the possible use of height compensators, sprung loaded features which are mounted onto suction cups to pick up items with height irregularity, such as packs of meat or blocks of cheese. These, like other options in the long list available to pick and place systems designers, need to be assessed at an early stage to ensure that the end effector combines with the robot itself to create a cost-effective, longlasting, reliable and trouble-free solution.
“Robotic devises are common place today and anyone can buy a robot arm,” concludes Paul, “however it’s the applications knowledge and ability to design the best possible solution for each application which is key and as always our philosophy is to be able to demonstrate the ability of robotics and end effectors at our ‘Try before You Buy’ facility.
Food manufacturers can attend a free educational event in June at Pacepacker’s Essex-based facility on robotics and automation where they will learn the differences between Cartesian, articulated arm and delta-style robots and their application capability.
Food manufacturers can use Pacepacker’s EEF award winning ‘Try Before You Buy’ facility to run product tests and trials. They are also hosting a free educational event in June, in Essex. For details contact Email events@pacepacker.com, Tel (0)1371 811544 or visit www.pacepacker.com.
*In the dairy category, vacuum handling can provide a great solution for product such as pots of yogurt, since it minimises contact and potential damage. But at the same time, the pack provides a secure seal with the gripper.
**One widespread application of clamp systems is in loading bags of root vegetables and other produce into bulk bins or trays. In this case, even high-suction vacuum tooling would not grip the product securely.