COVID-19 and the New ‘Norm’ for Manufacturing
©DesignPro
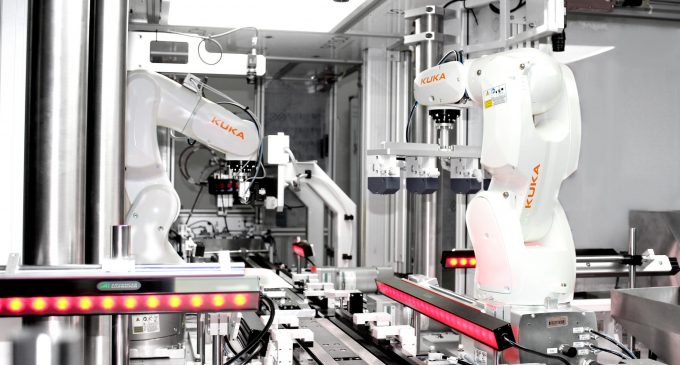
If ever a global crisis proved to remind us that an over-reliance upon scarce manual resources, and impractical overcrowded working conditions is unsustainable for the security of our supply chain and, survival of our manufacturing industries, the Covid-19 Pandemic has just surpassed it.
When eventually, our manufacturing sectors can return to work, the landscape will have completely changed. We must maintain social distancing within the workplace for the foreseeable future or until a vaccine is rolled out across the globe. Even then, social distancing within the workplace may become the new ‘Norm’ for manufacturing.
Critical finished goods manufacturing and supply chain has come under scrutiny during this pandemic and, many of the flaws in low-cost manufacturing in far-flung continents has come to the fore, with serious shortages in finished goods and raw materials arising. As a result, reshoring of manufacturing is inevitable, with many countries governments already issuing policy statements encouraging companies to reshore their manufacturing and supply chain, with several countries already offering substantial financial enticements for companies to do so. However, whilst this will undoubtedly be welcome news, cost competitiveness will be even more important. Automation and robotics will be fundamental to maintaining cost competitiveness.
Automation and the use of robotics is also set to become the new ‘Norm’ with increased focus upon reducing the concentrations of workers in close proximity to one another and, providing continuity of production even in the event of another major interruption to manufacturing and supply chain.
Sensitive and dexterous collaborative robots with small footprints will increasingly become our ‘co-Workers’.
The research will be accelerated to develop new applications for robotics; faster deployment, flexible and, easy to use.
Autonomous mobile robotics will become commonplace, not only in warehousing and logistics, but also in testing, sampling and, media preparation.
Cleanliness and hygiene will take on a whole new importance in the workplace and, whilst automated robotic sanitising in hospital environments is in early development, it may become necessary to consider similar technologies in manufacturing facilities.
Challenges
There are many challenges to be overcome in this new ‘Norm’ which requires collaboration and, initiatives across all invested parties including; the end user, regulatory authorities (e.g. ISO/FDA), government bodies, research institutions, universities, machine builders and, automation/robot suppliers. Including, but not limited to,
- Funded research – essential to develop new technologies.
- The skills Gap – already a critical shortage exists of automation and, robotics engineers across a range of skills levels from apprentice to master’s degree. This needs urgent addressing across our educational facilities, both for skilling and, upskilling.
- Workplace culture – operator acceptance of robot technology
- Brownfield Plant Design – not always suited to the deployment of automation. For example, the deployment of mobile robotics can easily be accommodated during the design phase for a greenfield facility but, may be more difficult in a brownfield facility where multiple floor levels, lifts, airlocks and, shared pathways were not designed with automation in mind.
- Government investment- support programs, particularly for smaller manufacturing companies and, solution providers.
- Agile Innovation funding
- Working capital loan schemes

Brian Cooney, General Manager KUKA Ireland
Summary
Robotics and automation companies, such as KUKA, have already risen to the challenge in the fight against Covid-19. Providing robotics to manufacture; Covid-19 test kits, automated sampling machines, PPE manufacture, automated temperature testing and, mobile disinfection robots.
As countries struggle to rebuild their economies, and manufacturing companies work to adapt to the new ‘Norm’ in manufacturing, robotics and automation companies will be there to help.
KUKA
KUKA is a global automation corporation with sales of around EUR 3.2 billion and around 14,200 employees. As a leading global supplier of intelligent automation solutions, KUKA offers its customers everything from a single source: from robots and cells to fully automated systems and their networking in markets such as automotive, electronics, general industry, consumer goods, e-commerce/retail and healthcare. The KUKA Group is headquartered in Augsburg, Germany. (31.12.2018)
KUKA Ireland are based in Dundalk.