Russell Finex Helps Nestlé Safeguard Product Quality at New 26,000 Tonnes/year Milk Powder Processing Plant in Chile
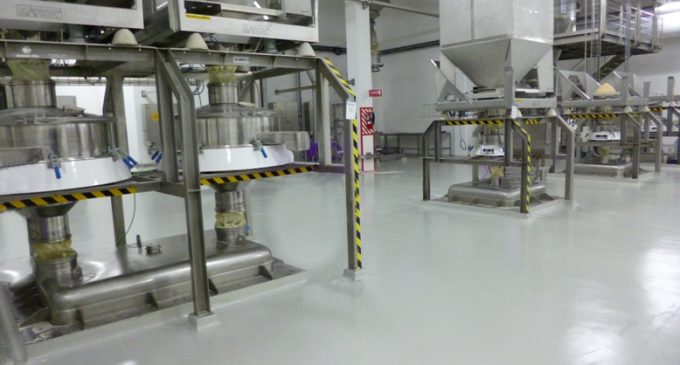
Six Russell Compact Sieve® units enable Nestlé to screen milk powder on finer meshes without compromising flow rates.
With factories or operations in almost every country, Nestlé is the world’s leading nutrition, health and wellness company. Since Nestlé first began selling in Chilein 1934, the country now provides one of the highest per capita consumption and sales of their products. Nestlé’s continued commitment to developing operations in the country, and a change in society for a healthier lifestyle leading to increased demand of milk powder products, have resulted in the investment of a new factory. Requiring the highest quality machinery, Russell Finex, a long term supplier to Nestlé, provided purpose built screening machines for the new plant.
The new factory, based in Osorno, is one of the most technologically advanced dairy factories of its kind. The factory produces a range of milk products with added nutritional value targeted not only at the domestic market but also at overseas markets, including theUnited States, Central America, the Middle East andAsia. Having strict Good Manufacturing Practices (GMP) and Hazard Analysis and Critical Control Points (HACCP) in place, Nestlé sought only the highest quality equipment for the new factory.
Having previously worked with Russell Finex at many of their factories worldwide, there was no hesitation in Russell Finex being the supplier of choice for their screening operations in the new factory. “The ongoing relationship is due not only to the high quality manufacture of all of Russell Finex’s separation equipment but also the accompanying documentation and certification that is provided”, states Jaime Sanchez, Maintenance Manager.
Traditionally rotary sifter screening machines have been used for the screening of powders. However this method of screening presents many problems. With the impeller forcing the powder through the mesh, product quality can be compromised as very little oversize is collected. In addition, most rotary sifters are supplied with nylon mesh which is prone to breakage. Therefore there has been a move to use gravity fed circular vibratory sieves as an alternative.
Following a consultation with a Russell Finex Sales Representative, it was decided that the Russell Compact Sieve® would best meet Nestlé’s requirements. With three different milk product ranges being processed, each requiring different flow rates, different sized Russell Compact Sieves®, comprising of 600mm, 900mm and 1200mm diameter units, were supplied to each process line.
Recent changes in industry practices have resulted in the need to screen milk powders finer. Traditionally 4mm aperture mesh (5 mesh) has been used but 2mm (10 mesh) is becoming more common practice. Unlike conventional vibrating screeners, the high performance Russell Compact Sieve® is able to screen the milk powder at this finer mesh size without compromising flow rates, preventing the sieve from becoming a bottleneck in the process. “We required a sieving system that would enable us to check-screen the milk powder to meet the standard set not only by Nestlé but also by Chile and the countries the milk powder is being exported to”, comments Sanchez. “With the industry moving towards 2mm screening, it was important to choose a sieve that would meet this criteria without slowing down the production process” continues Sanchez. The Russell Compact Sieves® have enabled the new factory to meet its target throughput rate of 26,000 tonnes/year.
All Russell Finex screening machinery is constructed in the highest possible quality stainless steel. The Russell Compact Sieve® is easy to clean between batches, and its simple design allows operators to strip down and clean the machines without tools. With enclosed screening for total containment, dust and fumes are also eliminated, not only helping Nestle to meet their strict zero dust environment policy, but also to improve operators’ health and safety. The machines were also fitted with BFM™ connectors, a unique innovation designed to provide a hygienic connector system, allowing for easy removal for cleaning or replacement.
Sanchez concludes, “The Russell Compact Sieves have not only helped us to meet our required capacity, but have also provided a hygienic solution that is mandatory for the milk powder industry”.
For over 75 years Russell Finex have manufactured and supplied filters, sieves and separators to improve product quality, enhance productivity, safeguard worker health, and ensure liquids and powders are contamination-free. Throughout the world, Russell Finex serve a variety of industries with applications including food, pharmaceuticals, chemicals, adhesives, plastisols, paint, coatings, metal powders and ceramics.